Is the maintenance of industrial machinery an expense or an investment?
Although the answer to this question seems obvious, there are still many people and even companies that constantly ask it.
Maintenance is one of the fundamental axes of any company, but especially in the industrial sector. Good preventive maintenance of machinery allows the production rhythm to be maintained, reduces accidents, increasing the safety of the equipment and, in the long run, reduces maintenance costs by avoiding failures and breakdowns.
Keep reading to learn about the concept of industrial maintenance, objectives, origin, types and benefits.
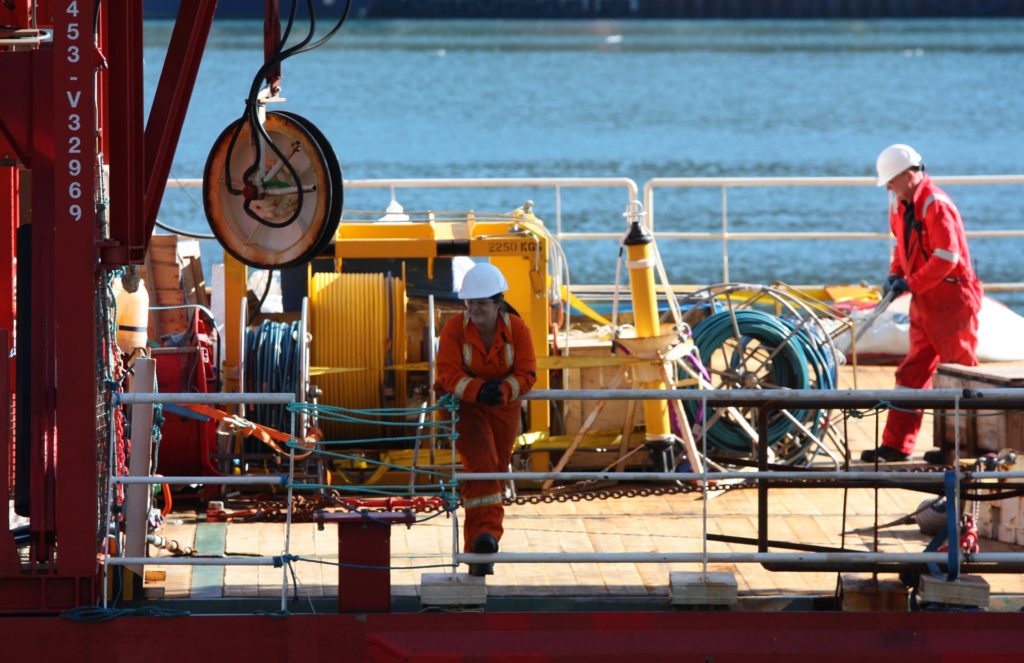
What is industrial maintenance?
In summary, industrial maintenance is the set of technical measures used to carry out maintenance or repair of equipment and machinery, and can be planned or unplanned.
With maintenance, the requirements for human, material, financial, and organizational resources are established to achieve the goals.
Its importance was consolidated in 1930 when Henry Ford opened an area in his company reserved for equipment repair.
The father of the modern production chain invested in the optimization of the maintenance department. For this, it hired experts in the prevention and detection of failures and breakdowns.
The objective was to guarantee the production process, avoiding the loss of raw material and the stoppage of the activity. There the concept of industrial maintenance was born as the constant monitoring of facilities and components, in addition to the repair and inspection of the functioning and good condition of a system.
Types of industrial maintenance
There are basically 5 types of maintenance, and the one or the most suitable for your industrial activity will depend a lot on the equipment and facilities that your company has.
It is important to clarify that it is not necessary to choose only one maintenance for your machinery. An adequate maintenance plan should consist of several modalities, depending on the type of machinery, the product or service they perform, the intensity of use, etc.
Corrective maintenance
It is a type of “reactive” maintenance, that is, it is applied when a problem arises and, as its name implies, consists of correcting errors that appear in the equipment due to wear and tear.
Usually it is not planned, unless the problem that arises is not very important and the equipment can continue to function, in which case its repair can be included at a later time, including the incidence in the company’s industrial maintenance plan.
Preventive Maintenance
This type of maintenance consists of carrying out a series of revisions and tasks systematically despite the fact that the equipment does not present problems or errors due to wear and tear or its habitual use, in order precisely to avoid future more serious breakdowns that avoid normal equipment operation and having to implement corrective maintenance.
Predictive Maintenance
It requires a timely industrial maintenance plan. It consists of constantly analyzing the equipment to determine if there is an alteration of the variables of the machinery.
For its application, it is necessary to carry out measurements of the equipment such as temperature level, energy consumption, vibration among other aspects.
By knowing the normal ranges, it is possible to detail with greater precision some type of alteration that causes problems and predict possible failures in the future.
It is one of the types of advanced industrial maintenance as it requires the use and knowledge of various tools such as computer science, analysis of results, mathematics, chemistry and calculation.
Zero hour maintenance
It serves to extend and guarantee the useful life of the devices. It consists of applying a series of procedures that leave the machine “to zero” that is, as if it were new, eliminating or replacing all the elements that may have suffered some kind of wear and tear.
It can be done when the equipment loses its performance or when it still works without any inconvenience.
Maintenance in use
It is the most basic and very low-intervention type of maintenance, usually performed by equipment operators or non-specialized personnel.
It is done with simple prevention tasks, such as cleaning or reporting visible defects that must be taken care of by someone with more experience.
Objectives of industrial maintenance
Although in general lines, the objective of industrial maintenance is to keep it in operation in a stable way and reduce the number of incidents, accidents, and breakdowns, there are other objectives and benefits associated with the correct maintenance of the equipment. Here we list some of them:
- Reduce incidents that may cause the unexpected stoppage of production equipment.
- Maintain the production capacity of the machinery.
- Increase work productivity.
- Allow machinery to work without stopping, that is, with the highest efficiency and least wear, and thus prolong its useful life.
- Ensure the operation of production equipment at a minimum cost.
- Avoid workplace accidents by handling equipment.
Industrial maintenance, cost or investment?
The most innovative companies acquire equipment for the monitoring of machinery, which allows them to carry out predictive maintenance, making an initial investment with the aim of reducing future costs, either in the form of expensive repairs or production losses.
In these cases, senior management makes an investment in the purchase of the equipment, which becomes part of the assets of the company.
Undoubtedly, the application of strategies aimed at the implementation of preventive and predictive maintenance has a positive impact on operating times.
In this sense, according to statistics, there is an acceptable range of disbursement for this concept, which is located at 25% and 35%. Outside these limits, uncontrolled expenses are considered due to the increase in failures due to the lack of maintenance in use until the predictive one.
In this sense, it is important to determine what is the limit that a company can tolerate for it to consider that there is excessive spending that puts a risk on the company’s profit margins.
If a correct maintenance policy is applied, the costs for this concept should be less and less
For this, the company must include as a policy that if the equipment is new, it also requires attention to ensure its operation.
When the financial managers observe that the application of the maintenance plans are transformed into savings, they do not hesitate to invest.
Our recommendation from Proteval is that you have to plan and monitor the strategy that results in greater efficiency of the investment in maintenance and therefore in the benefit of the entire company.
The value of predictive and preventive maintenance reduces the high costs of corrective maintenance or worse, the stoppage of production.
You have to differentiate between an expense and a cost, the latter is reflected in a short or long-term investment.
In this case, the department in charge of industrial maintenance must be clear about the capital investment plan and the return on investment or ROI.
The above is translated as follows:
If the company is working with 40% efficiency and considers that it can increase 10 points to take it to 50% with a greater investment in maintenance, do it!
It will be reflected in the 25% increase in capacity and therefore the financial justification is clear. In conclusion, maintenance is an investment and not an expense.
Conclusion
- Industrial maintenance is the action that is carried out periodically to guarantee the performance of machinery and facilities.
- Poor maintenance can have a major impact on production.
- Maintenance is the heart of the industry and therefore must be treated as a priority.
- Companies that implement maintenance systems have a great competitive advantage.
- It is essential to hire the services of industrial maintenance professionals to carry out this work.
- To reduce operating costs and increase the return on investment, it is necessary to guarantee the operation of the equipment.
- Predictive and corrective action is essential for any industry because it minimizes expenses and increases business profitability.
Taking all this into account, maintenance can and should be considered an investment and not an expense.