Waterjet Cutting, How it works
As we said in a previous post, the team to carry out the Water Jet Cutting would be composed mainly of two key rooms, the Technical Office and another where the Workshop or logistics center would be located.
“The intention now is to explain the operation of this revolutionary machine, which from Proteval in Aldaya (Valencia, Spain), we recommend as it is a very versatile tool and whose application can be extended to practically all industrial jobs.”
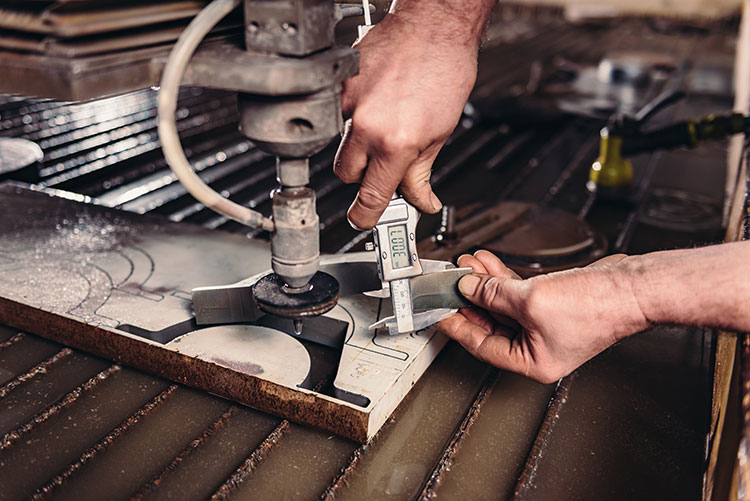
Operating Process
The first phase of the process is executed when the order reaches the technical office, here the part is designed on the computer specially configured for it, assigning the measurements of the object, its thickness and the type of material to be cut.
Once the part to be machined is designed, a reference is added to it, and this is linked to the particular program of the waterjet cutting machine.
The second phase, in the database, through the machine’s own computer, the previously saved file is searched, wherein we can add certain data such as:
- The hardness or characteristics of the material.
- The type of cut you want to obtain, since it can vary from the grossest to the most defined, since the edges of the cut are clean and with no imperfections.
“This process will depend on the utility you want to give to the piece, in addition to its importance or the price that the customer is willing to pay.”
When we have already decided on the design to be made, the process of adjusting and fixing the blank to be cut would begin, in which we would have two important parts:
- The first phase, the distribution of the material must be taken into account in order to optimize it.
- The second phase, the available material has to be valued, whether it is remains of other machining or material to be used, always trying to take advantage of the stock in order not to accumulate remains of some and other jobs, thus reducing costs and making the material we have profitable.
The Water Jet Cutting Machines can operate simultaneously on different pieces, since their correct location allows, in the case of machines with multiple cutting heads, to work in parallel and thus speed up the cutting process, being able to work with different assignments.
- The Third phase would consist of cutting the piece, in which once the First and Second phases were prepared, the machine would take command of the operation.
There is the possibility of having to interrupt the process if we intend to readjust the part, or to check if the process is correct, but if there is no readjustment problem, from the time the machine starts the cut to the end, we would obtain a continuous process that ends with an excellent finish of the piece to be machined.
Process characteristics
The machinery itself consists of a jet of water under pressure.
Its nozzle diameter ranges from:
0,08 mm a 0,45 mm diameter |
Through which water or a mixture of water comes out together with the abrasive, launched at a very high pressure, capable of cutting any type of material.
One of the most important elements is the nozzle through which the jet comes out; since the cohesion and to a large extent the applied technical feasibility depend on this, since if the jet is conical, cutting power, quality, precision, and dry cutting characteristics are lost.
The pressure of the water jet is another of the most important characteristics of the process
It is provided by a system consisting of a pump equipped with an ultra-pressure intensifier that allows it to reach up to 4000 bars of pressure.
There is the possibility of working at high pressures, although many times it is not necessary due to the thickness to be cut, with much less pressure the same cut would be made and with the same conditions.
What makes it work normally at maximum pressure is the fact that it streamlines the process as this makes cutting faster, which can take from minutes to hours.
Depending on the object to be cut, there is the option of working at a lower pressure (around 2000 bars) or even working without the abrasive; since this is used in materials of little hardness that do not need the abrasive to be cut, or to workpieces that only have to be marked, not cut.
The metal signs in which the letters and figures embodied are also made with low-pressure water jets, would not be cut but marked, obtaining surprising results.
Cutting speed is of utmost importance
This will depend on factors such as the pressure of the pump and the capacity of the intensifier, the diameter of the nozzle, quantity and quality of abrasive and the thickness of the piece.
The speed values that this entire pressure supply system tolerates, allows the liquid to exit through the orifice at a speed of 1000 meters per second.
Adding abrasive to the water is due to the fact that a simple jet of water would not be able to develop cuts in the hardest materials, with the mixture of clays and glass it would give the system an infinite increase in cutting possibilities.
The thickness of the piece to be cut
From a thickness of 5 mm | When would it become profitable to use this method? |
Up to the thickness of 200 mm | In any material. |
Even reaching 400 mm | Using the special application. |
This water jet can cut all types of materials, from metallic to soft, it is even used for surface preparation such as boat cleaning, automotive paint or the aerospace industry.
It is a process in which the generation of polluting particles is minimal, it does not provide surface oxidation and the generation of chips is non-existent.
As a characteristic of Water Jet Cutting, it should also be noted that the process does not affect the materials since it does not harden or deform them, being a method that in various cases is more useful than laser or plasma when working requires a good finish.
“At Proteval in Aldaya (Valencia) we consider that this cutting method represents a revolutionary advance in the face of the worker’s self-safety and the work carried out, the latter having a good finish without a doubt for practical purposes.”